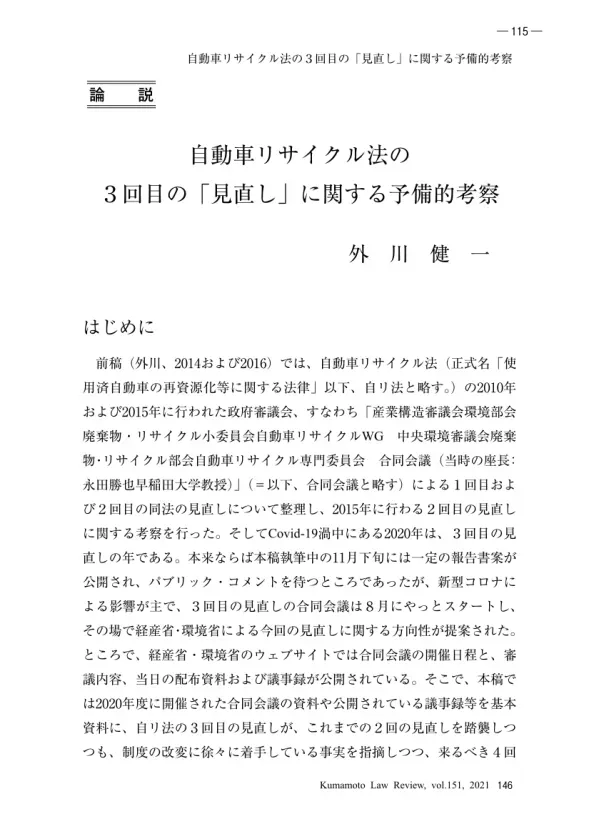
自動車リサイクル法改正:現状と課題
文書情報
著者 | 外川健一 |
学校 | 早稲田大学 (推定) |
専攻 | 機械工学、資源工学関連 (推定) |
文書タイプ | 論説 |
言語 | Japanese |
フォーマット | |
サイズ | 1.89 MB |
概要
I.日本の自動車リサイクル制度の現状と課題 ASR 処理を巡る問題
本稿は、日本の自動車リサイクル法(ASR:Automobile Shredder Residue問題を含む)の現状と課題を分析する。2018~2019年の政策転換により、ASR処理価格の高騰、首都圏を中心に自動車リサイクルシステムの機能不全が発生。破砕業者による廃車ガラ引き取り制限も問題化。中国への輸出規制強化により国内処理負担が増大し、再資源化施設の処理能力逼迫、リサイクル率低下につながっている。遠距離差配の問題も深刻で、鉄リサイクル工業協会のアンケートでは年間約3600万円の損失が報告されている。
1. 自動車リサイクルシステムの機能不全
2020年8月19日の第48回合同会議では、経産省産業構造審議会・自動車リサイクルWGの座長が永田勝也氏から村上進亮氏へと交代したことが報告されました。この人事は、日本の自動車リサイクル政策における大きな転換点であり、2018年から2019年にかけて顕著になった問題の背景を理解する上で重要です。具体的には、政策転換の結果、行き場を失った雑品類がシュレッダー処理され、自動車由来のASR(Automobile Shredder Residue)とその他の鉄源を砕いた破砕くず(SR:Shredder Residue)の処理価格が高騰しました。その結果、破砕業者が解体業者からの廃車ガラ(解体自動車)の引き取りを制限し、首都圏を中心に自動車リサイクルシステムが機能不全に陥る事態が発生しました。これは、法施行当初目指されていた『どのような経済状況でも安定的に機能する自動車リサイクルシステム』とは大きく異なる状況です。この事態は、リサイクルシステムの脆弱性と政策変更の影響を如実に示しています。
2. 中国輸出規制強化と国内処理能力の逼迫
中国等の外国政府による輸入規制・輸入制限強化は、日本の自動車リサイクルシステムに深刻な影響を与えました。これまで中国などに輸出されていたプラスチックくずや雑品スクラップを国内で処理せざるを得なくなったため、65再資源化施設として認定されている焼却施設などに廃プラスチックが殺到し、処理能力が逼迫しています。さらに、65再資源化施設の事故による受け入れ停止や、大規模災害の発生なども重なり、リサイクル率は低下し、直接埋立や廃棄物の引取時期調整といった事態に陥っています。この状況は、安定的なリサイクルシステムの構築を阻害する大きな要因となっており、早急な対策が必要であることを示唆しています。特に、ASRの遠距離輸送は温室効果ガス排出量の増加にも繋がるため、その実態解明と改善策の検討が喫緊の課題として挙げられています。
3. 遠距離輸送コストと損失の現状
鉄リサイクル工業協会による2019年のアンケート調査では、自動車メーカーによるASRの遠距離輸送が常態化していることが明らかになりました。例えば、北海道で発生したASRを富山県の再資源化施設へ輸送したり、その逆のケースも見られました。この遠距離輸送に伴う運賃補助がコストに見合わないケースも多く、多くの事業所で大きな経済的損失が発生しています。アンケート調査では、廃自動車を破砕し遠方差配を行う34事業所のうち97%にあたる33事業所で、年間で延べ約3600万円の損失が出ていると報告されています。この結果は、効率的なリサイクルシステム構築の妨げとなり、コスト構造の見直しが必要であることを強く示唆しています。適正なリサイクルの推進は重要ですが、現状のシステムでは経済的持続可能性が危ぶまれます。
II. 31条認定全部利用 と 非認定全部利用 リサイクル手法の比較
ASR削減のため、31条認定全部利用(解体業者による精緻な解体、鉄鋼メーカーへの直接納入)と非認定全部利用(市場原理による売買、輸出を含む)の2つの手法が存在する。31条認定全部利用はASR削減に有効だが、近年停滞している。一方、非認定全部利用、特に輸出においては、有害廃棄物の海外流出リスクがあり、その実態解明が急務である。東京製鐵は、2013年からAプレスの受け入れを開始し、徐々に利用量を増やしている。
1. 31条認定全部利用 ASR削減に向けた取り組み
自動車リサイクル法の31条に規定された『認定全部利用』は、シュレッダーダストの発生を抑制する有効な手法として注目されています。この方法は、破砕業者を介さずに、解体業者が精緻な解体を行い、廃車ガラ(プレス加工したAプレスを含む)を直接鉄鋼メーカー(主に電炉メーカー)に納入する仕組みです。特に、粗鋼生産における不純物である銅を除去するために、ワイヤーハーネスやモーターなどを事前に取り外し、非鉄スクラップディーラーに販売することで、銅分0.3%以下の高品質な廃車ガラやAプレスを鉄鋼メーカーに供給できる点が特徴です。この手法は、自リ法施行当初は全体の約10%程度の割合で行われていましたが、近年は停滞しています。しかし、ASR再資源化施設の稼働が不安定な現状を踏まえれば、認定全部利用の更なる推進は有効な手段と言えるでしょう。このシステムでは、ASRを出さない努力をした解体業者に対して、ASRリサイクル料金の一部が支払われます。ただし、2003年の経産省・環境省タスクフォースの見解に基づき、解体業者への払い戻し額は預託されたASRリサイクル料金よりも安価でなければなりません。東京製鐵は、法施行当初は消極的でしたが、Aプレスの品質が安定したと判断してから、2013年から自動車Aプレスの受け入れを開始し、徐々に利用量を増やしています。
2. 非認定全部利用 市場原理と輸出リスク
一方、『非認定全部利用』は、解体業者または破砕業者がASRリサイクル料金の返還というインセンティブに頼らず、廃車ガラ(またはAプレス)を市場原理のみで鉄鋼メーカーなどに売買する手法です。この手法には、国内の鉄鋼メーカーなどに引き渡されるものと、海外へ鉄源として輸出されるものの2種類があります。近年、注目されているのは、破砕段階からの非認定全部利用・輸出が急増している点です。鉄リサイクル工業協会は、第50回合同会議で、輸出されたAプレスのシュレッダー処理後のASR処理実態が不明であり、ASRに該当しない有害廃棄物が海外に流出する可能性も否定できないと指摘しました。これは、かつての雑品輸出における問題と同様、中国以外の海外市場への潜在的な廃棄物輸出が行われている可能性を示唆しています。したがって、非認定全部利用による輸出の実態を明らかにし、廃棄物の輸出が行われていないか検証することが不可欠です。一部の破砕業者は東南アジアのスクラップディーラーと連携して安定的な鉄源供給を目指していますが、全体として廃棄物輸出の問題を無視できないため、徹底的な検証が必要です。
III.リサイクル料金の運用と 解体インセンティブ制度 の提案
自動車リサイクル制度では、製造業者等がASRの全量引き取りを担うが、解体業者や破砕業者へのインセンティブが不足している。リサイクル料金の運用についても、高額なシステムコストやユーザー負担の公平性の問題が指摘される。2020年11月の第51回合同会議では、解体インセンティブ制度(ASR削減に貢献する解体業者への経済的インセンティブ付与)が提案された。この制度は、31条認定全部利用と同様のコンソーシアム構築を想定するが、樹脂やガラスの再資源化業者が限られている点が課題。
1. リサイクル料金制度の問題点 高コストと公平性の課題
日本の自動車リサイクル制度では、自動車製造業者等がASR(Automobile Shredder Residue)を全量引き取る仕組みとなっており、その費用はリサイクル料金から賄われています。しかし、この制度にはいくつかの問題点が指摘されています。まず、リサイクル料金の設定単位に課題があり、約15年後の廃車時の費用を様々な変動要素を加味して設定するため、徴収費用と実費に差が生じ、メーカーの収支が黒字になるケースも発生するなど、ユーザーの適正・公平な負担を担保することが困難です。さらに、廃車時まで車台番号別にリサイクル料金(総額9000億円)を管理する必要があるため、システム面・管理面での多大なコストが発生しています。初期システム構築費用は約200億円、年間維持費用は約24億円にも上ると試算されており、この高コスト構造は、日本の自動車リサイクルシステムが先進国から「High Cost Recycling」と揶揄され、ガラパゴス化している一因となっています。また、自動車リサイクル促進センターを管理主体とする点についても、事故発生時の特預金の増加にも関わらず、ユーザーへのリサイクル料金・手数料の低減に反映されていない点が問題視されています。これらの問題点は、制度の抜本的な見直しを迫るものです。
2. 解体業者 破砕業者へのインセンティブ不足と再資源化の高度化
自動車リサイクル制度において、自動車製造業者等がASRを全量引き取るという構造は、解体業者や破砕業者によるリユース・リサイクルに対するインセンティブを弱めているという指摘があります。彼らの積極的な取り組みを促すためには、より効果的なインセンティブが必要となります。破砕・選別の精度向上によるプラスチックやガラス等の素材回収の取り組みもなされていますが、事業採算性に課題があり、十分な成果は得られていません。環境配慮設計や部品リユースの促進、Car to Carリサイクル、そして業種間の連携強化など、3R(Reduce, Reuse, Recycle)に係る取組の高度化が求められています。こうした状況を踏まえ、2020年11月20日の第51回合同会議で提案されたのが「解体インセンティブ制度(仮称)」です。これは、ASRの削減と再資源化の高度化を目的として、素材回収に取り組む解体業者等に、預託されたリサイクル料金を原資とした経済的インセンティブを付与する制度です。具体的なスキームは、31条全部利用と同様にコンソーシアムを構築し、再生樹脂・ガラス製造業者等との連携の下、適切な再資源化が行われた場合に、ASRリサイクル費用の一部を解体業者に分配するというものです。
3. 解体インセンティブ制度の課題と今後の展望
解体インセンティブ制度はASR削減に有効な手段と考えられますが、樹脂やガラスの再資源化業者が限られているため、適切な競争原理が機能するかが課題です。特に、ASRリサイクル料金の削減分しかインセンティブが与えられない仕組みでは、解体業者に廃プラの再資源化を十分に促すインセンティブとはなりえない可能性があります。つまり、解体業者の手間賃に見合うだけのインセンティブが提供できるかどうかが不透明です。さらに、自動車由来のガラス、特にフロントガラスなどの合せガラスは産業廃棄物として処理費用が発生する点も課題です。一部のサイドガラスは自動車ガラスや建物ガラスへの再生、その他はグラスウールへの再生が期待できますが、これらの点も考慮して制度設計を行う必要があります。 安定的なASRの再資源化のためには、適切なコストをきちんと支払うことが重要であり、解体インセンティブ制度の具体的な仕組みを検討していく必要があります。
IV.再資源化の高度化 ASR 削減と素材回収の課題
再資源化の高度化においては、破砕・選別精度の向上によるプラスチックやガラス等の素材回収が重要となる。しかし、事業採算性、特に塗膜剥離技術の未確立が課題。いその株式会社は、塗膜剥離をせずに自動車バンパーを内装材にリサイクルする手法に挑戦している。また、炭素繊維強化プラスチック(CFRP)の処理方法として、サーマル・リサイクルが有効とされている。
1. ASR削減と再資源化高度化に向けた取り組み
自動車リサイクル法では、自動車購入者がASR(Automobile Shredder Residue)の再資源化費用を負担し、製造業者等がその責務を負うことで、使用済自動車が安定的にリサイクルされる仕組みとなっています。しかし、通常の廃棄物と異なり、処分コストによるリユース・リサイクル促進効果が期待できない点が課題です。2020年8月19日の第48回合同会議資料7では、再資源化の高度化が重要な課題として挙げられています。特に、破砕・選別の精度向上によるプラスチックやガラス等の素材回収が注目されていますが、事業採算性への懸念が示されています。第51回合同審議会資料4では、ASRの削減と再資源化の高度化を目的とした、素材回収に取り組む解体業者等への経済的インセンティブ付与制度が具体的に提案されています。これは、預託されたリサイクル料金を原資とし、解体業者と再生樹脂・ガラス製造業者などがコンソーシアムを構築し、使用済自動車から樹脂やガラスを適切に取り外し再資源化することで、ASRリサイクル費用の一部を解体業者に分配する仕組みです。従来はASRに含まれることを容認してきた廃プラ・廃ガラス類が取り除かれることでASR削減効果も期待できます。
2. 樹脂 ガラス再資源化の課題とインセンティブ設計
提案されている解体インセンティブ制度はASR削減に有効な手段として期待されますが、樹脂やガラスの再資源化業者が限られている点が課題として挙げられています。そのため、適切な競争原理が機能するかが問われます。特に、ASRリサイクル料金の削減分のみをインセンティブとする制度では、解体業者に廃プラの再資源化を促すだけの金額が支払われるとは限りません。解体業者にとって、手間賃に見合うインセンティブが提供されるかどうかも不透明です。さらに、自動車由来のガラス、特にフロントガラスなどの合せガラスは産業廃棄物として処理費用が発生するという課題も残されています。一方、一部のサイドガラスは自動車ガラスや建物ガラスへの再生、その他はグラスウールへの再生が期待できるため、これらの可能性も考慮した制度設計が必要となります。 宇部興産など、自動車由来の樹脂再資源化事業に参入した企業も撤退している現状も考慮する必要があります。塗膜剥離技術の未確立が、大きな障壁となっています。
3. CFRP処理とサーマルリサイクル
車体軽量化のために使用される炭素繊維強化プラスチック(CFRP:Carbon Fiber Reinforced Plastics)の適正な処理方法も構築する必要があります。J-Farによる委託事業で矢野総合研究所が報告書を公開しているように、CF含有ASRを炭化炉でブリケット化し、電炉で燃料として使用するサーマル・リサイクルが、現時点でもっとも有効な処理方法と考えられています。この手法は、ASR削減と同時に、廃棄物処理コスト削減にも貢献する可能性があります。しかし、CFRPのサーマルリサイクルが、経済的にも環境的にも本当に最適な方法であるか、さらなる検証が必要です。また、いその株式会社が環境省やJ-Farの公募事業を通じて、塗膜剥離をせずに自動車バンパーを内装材にリサイクルする手法の確立に挑戦しているなど、様々な技術開発が行われています。これらの技術開発の現状と将来性も、再資源化高度化の議論において重要な要素となります。
V.次世代自動車への対応 バッテリーリサイクルと Right to Repair
ハイブリッド車や電気自動車の普及拡大に伴い、リチウムイオン電池のリサイクルが課題となっている。中古車輸出比率の高さが、国内施設の整備効果を限定する。Right to Repair(修理する権利)の考え方は、自動車部品のリユースを促進する上で重要だが、日本の強固な部販・共販システムと電子部品の電子ロック化が課題となっている。ポーランドの解体業者団体FORSのオンライン会議では、インフォーマルセクターへの使用済み自動車流出が懸念されている。
1. 次世代自動車におけるバッテリーリサイクルの現状と課題
ハイブリッド車、電気自動車、燃料電池自動車など次世代自動車の普及拡大に伴い、大容量・高電圧バッテリーや水素タンクなど、従来の内燃機関車にはなかった部品・素材のリサイクルが新たな課題となっています。自動車リサイクル法では、車載用電池は解体時に取り外すこととされており、リユースや廃棄物としての回収・リサイクルが行われています。しかし、リユース・リサイクルに係る技術や手法は現在開発途上であり、特にリチウムイオン電池の処理技術確立が急務です。2020年度には、自工会により新たに5事業所がリチウムイオン電池リサイクル施設として認定されましたが、阿部(2020)の指摘するように、2017年度のデータでは、日本のハイブリッド車抹消登録台数の75~91%が中古車として輸出されており、国内で整備されたリサイクル施設の利用は限定的です。これらの施設は、あくまでもセーフティネットとしての機能が主であり、海外でのELV(End-of-Life Vehicle)発生と処理の問題を考慮する必要があります。 特預金や剰余金の活用も視野に入れるべきでしょう。
2. CFRPの処理とサーマルリサイクルの可能性
車体軽量化のために使用されている炭素繊維強化プラスチック(CFRP: Carbon Fiber Reinforced Plastics)についても、適正な処理方法の構築が課題です。J-Farによる委託事業で、矢野総合研究所が報告書を公開しています。2019年度の第47回合同会議資料6では、CF含有ASRを炭化炉でブリケット化し、電炉で燃料として使用するサーマル・リサイクルが、現時点ではもっとも有効な処理方法であると報告されています。この手法は、ASRの削減に貢献するだけでなく、燃料としての利用という新たな価値創出の可能性も秘めています。しかしながら、このサーマルリサイクルが経済性や環境負荷の面で本当に最適な方法であるかは、更なる検討が必要です。今後、CFRPの処理技術の進歩や、新たなリサイクル技術の開発状況を注視していく必要があります。
3. 自動車部品リユース阻害要因 電子ロックとRight to Repair
自動車部品の電子化は、自動車部品のリユース促進を阻害する要因となっています。盗難車由来の中古部品の不正使用を防ぐため、自動車メーカーが電子ロックをかける部品が増加しており、これにより、リサイクル部品の再使用が困難になっています。この問題は、日本の解体現場ではまだほとんど報告されていませんが、ドイツの中古車が多く輸入されているポーランドでは、既に深刻な問題となっています。先進国の自動車解体業者は、この問題に関してWTOに陳情している状況です。一方、米国マサチューセッツ州で成立した「Right to Repair」法は、自動車メーカーによる補修用部品の供給制限を禁止し、修理情報を公開することでユーザーの修理権を保護するものです。この考え方は、EU指令の見直しを担当するEU政府担当官も重視しており、日本の部販・共販システムの現状と比較検討する必要があります。日本の独立系整備業者は、この状況下でますます窮地に立たされていると言えるでしょう。